2012 Scm Integra System
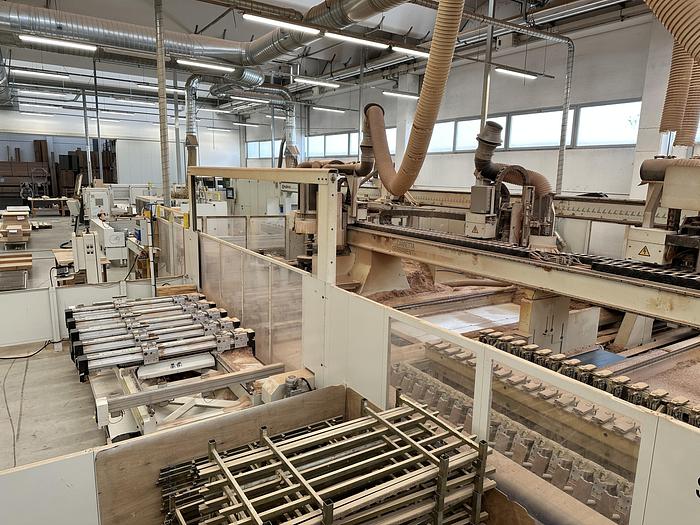
Specifications
Manufacturer | Scm |
Model | Integra System |
Year | 2012 |
Stock Number | MGR016 |
Description
Integrated NC machining center for windows and doors composed of: A) Automatic loader mod. "SP" Automatic loader for Base SP N. 1 moulder -Automatic loader consisting of: -Table with motorized belts -Automatic device for moving pieces from the buffer to the loading surface of the moulder * Piece length min: 450 mm max: 3200 mm * Piece width min: 40 mm max: 230 mm * Piece thickness min: 40 mm max: 120 mm * Work cycles 10/min * Chain advancement speed on the table: 7 m/min * Loading table dimensions 2800 x 2150 mm B) Automatic moulder mod. SUPERSET NT C 6 Position 1 = Planer Shaft Position 2= 1st right vertical shaft Position 3= 1st left vertical shaft Position 4= 1st upper horizontal shaft Position 5= 1st lower horizontal shaft Position 6= Group for slat recovery 2500 mm entry level Speed 6-36 m/min via inverter No. 1 - engine power 5.5 hp (4 kw) Horizontal presser before the planer with pneumatic exclusion from the panel Pneumatic exclusion from the control panel for the feed unit located before the planer shaft Tandem advance group in front of the right vertical with rapid exclusion Advance groups after the upper ones for reducing the towing distance from 620 mm to 450 mm Input guide with bearings for automatic feeders Electrical predisposition for the use of automatic loaders Manual centralized lubrication Pump for lubrication of the work surface with automatic drive Setup for in-line integration with INTEGRA SYSTEM - work surface raised to 970 mm - traffic light at entrance - piece counting Independent electrical panel POS. 1 High precision shaft 10 hp (7.5 kw) engine instead of 5.5 hp (4 kw) Brake for engines from 5.5 hp (4 kw) to 10 hp (7.5 kw) T-SET quick tool locking -allows tool locking/unlocking with the simple use of a compressed air gun POS. 2 High precision shaft 10 hp (7.5 kw) engine instead of 5.5 hp (4 kw) Brake for engines from 5.5 hp (4 kw) to 10 hp (7.5 kw) Vertical shaft with a useful length of 180 mm T-SET quick tool locking Electronic vertical positioning POS. 3 High precision shaft 10 hp (7.5 kw) engine instead of 5.5 hp (4 kw) Brake for engines from 5.5 hp (4 kw) to 10 hp (7.5 kw) High precision shaft Vertical shaft with a useful length of 180 mm T-SET quick tool locking Electronic horizontal positioning POS. 4 High precision shaft 10 hp (7.5 kw) engine instead of 5.5 hp (4 kw) Brake for engines from 5.5 hp (4 kw) to 10 hp (7.5 kw) Rotation speed 8300 rpm T-SET quick tool locking Electronic vertical positioning POS. 5 High precision shaft 10 hp (7.5 kw) engine instead of 5.5 hp (4 kw) Brake for engines from 5.5 hp (4 kw) to 10 hp (7.5 kw) Rotation speed 8300 rpm T-SET quick tool locking POS. 6 Glass bead recovery group Comprehends: PRL allows the automatic transition from planing to function recovery of the glazing bead and vice versa. - operating group with shaft diameter 30 mm, length 30 mm - electronic horizontal positioning - electronic vertical positioning - hardware and PLC modifications for axis management - tandem exit and modified hood second advancing group after the universal C) Connection transfer Transfer for receiving pieces from the moulder and automatic insertion into the Sotto Sopra DMC sander Complete with lateral chute for unloading cut glass bead strips on the moulder. Designed to manually load blind pieces with widths from 70 to 700 mm Transfer consisting of: - Motorized roller conveyor dim. 800 x 6000 mm - Motorized belt table dim. 2700 x 6000 mm: complete with section equipped with pneumatic movement for roller-belt piece transfer - Motorized roller conveyor dim. 2800 x 1500 mm complete with motorized cross belt frame equipped with movement vertical pneumatic belt-roller piece transfer. Transversal motorized guide for inserting pieces Sander in ladder position. D) Compact sanding calibration line SOTTO/SOPRA mod. SYSTEM BT44CC 1350 RRD + RRD LOWER GROUPS MOD. B4C 1350 RRD BASEMENT * Fixed workpiece passage height at 900 mm from the ground * Insertion of ribbons from the left side of the machine * Main engines inside the base ADVANCEMENT BENCH * Motorized adjustment of the work surface with two-speed gear motor * Rear rubber-coated carpet drive roller * Device for automatic centering of the conveyor belt * Input safety microswitch for excess thickness * Useful working widths 1350 mm * Min. thickness and max. workable 3 ÷ 170 mm * Feed speed from 3.5 to 18 m/min OPERATING GROUPS * Belt oscillation with electronic control * Automatic disc brakes for quick stopping of groupsets PRESSURE SETS * Inlet grooved rubber roller equipped with safety device to prevent pieces from returning ELECTRICAL EQUIPMENT * Automatic star/delta starting on the main engine * Magnetothermic protections on motors * Stabilized current power supply for electronic equipment "Hydra V-Pad" CONTROL PANEL * PLC terminal with color LCD display" * Touch screen functionality * Graphic display of the machine configuration * Machine management from touch screen, manually or through 120 configurable work programs by the user * Engagement/disengagement in working position and timing of the roller groups * Management and control of the belt advancement speed * Management and control of the working thickness * Automatic sequential start-up of the main engines * Activation and control of the timing of the belt cleaning blowers * Management of the windowed pieces recognition program * Machine operation report (working hours/on hours) * Management of machine failure alarms and fault diagnosis on the electronic boards * Management of machines in compact line configuration EMERGENCIES / SAFETY * Hand protection strap at entry of pieces * Front and rear emergency mushroom switch * Lockable main switch * Automatic emergency stop of the machine in case of: - breakage of the abrasive belt - non-tensioned abrasive belt - lateral exit of the abrasive belt - opening of the access doors to the operating groups - lack of compressed air - motor overload SY B4C 1350* CARRYING BASE * * Control panel on the machine 1st OPERATING GROUP “R” R-CL 1350 * Calibrator/sanding roller assembly The group is equipped with: * Adjustment of the working position of the roller with indicator and pre-selection memory of the abrasive belt grain * Automatic disc brake for stopping the sanding belt in case of emergency * Automatic oscillation of the abrasive belt via electronic system * Abrasive belt rotating in the opposite direction to the advancement - Development of abrasive belt 1900 mm R250 Roller diameter 250 mm R85 85 sh rubber coated calibrator roller with abrasive belt speed of 24 m/sec Pneumatic ON/OFF of the roller made with a pneumatic activation cylinder complete with micrometric adjustment of the position of the roller depending on the thickness of the abrasive belt Oscillating blower for cleaning the longitudinal abrasive belt The device is equipped with: - Operation of the swing with electronic system - Timed intervention activated directly by the piece being processed - Filter and pressure regulator 11 kW (15 HP) motor 2nd OPERATING GROUP “R” R-CL 1350 * Calibrator/sanding roller assembly The group is equipped with: * Adjustment of the working position of the roller with indicator and pre-selection memory of the abrasive belt grain * Automatic disc brake for stopping the sanding belt in case of emergency * Automatic oscillation of the abrasive belt via electronic system * Abrasive belt rotating in the opposite direction to the advancement - Development of abrasive belt 1900 mm R250 Roller diameter 250 mm R65 65 sh rubber coated calibrator/sander roller with abrasive belt speed of 18 m/sec Pneumatic ON/OFF of the roller made with a pneumatic activation cylinder complete with adjustment micrometric of the position of the roller as a function of the thickness of the abrasive belt Oscillating blower for cleaning the longitudinal abrasive belt The device is equipped with: - Operation of the swing with electronic system - Timed intervention activated directly by the piece being processed - Filter and pressure regulator 11 kW (15 HP) motor 3rd OPERATING GROUP “D” DP 4/16 1350* TRANSLATING PLANETARY GROUP WITH 4 HEADS ROTARY ABRASIVE BRUSH HOLDER Prepared for housing 16 brush discs with a diameter of 125 mm. SI/8/125 * Set of 16 rotary discs with a diameter of 125 mm SI/8/125 * Complementary set of 16 discs with a diameter of 125 mm Electronic auto-set of the "DP 4/16" group for work positioning managed by the Hydra V-Pad electronic control 4th OPERATING GROUP “b” GS/200 1350 * BRUSH ASSEMBLY The device is equipped with: - Dust extraction hood - Adjustment of the working position of the roller - Rubberized pressure roller at entry and exit Cleaning roller with a diameter of 200 mm in Tampico 1.1 kW (1.5 HP) main motor · PRESSERS GP/M-E Pressure group with rubberized rollers and tip at entry to the 1st roller group GP/M-I Pressure group with rubberized rollers and intermediate tip between the 1st and 2nd roller group GP/M-U Pressure group with rubberized rollers and tip exiting the 3rd roller group · WORK PLAN Carpet advancement with 3 kW inverter 60 sh rubber conveyor belt · COMPACT IN-LINE MACHINE DEVICES Machine in compact start-of-line version (lower/upper) with System T4C 1350 following. The entire compact line is managed by a single "Hydra V-Pad" control panel and a single "PLC" ELECTRONIC CONTROL 10.4" touch-screen monitor for Hydra V-Pad PLC X-20 control panel Modular hardware structure for managing machine functions from the "Hydra" control panel. UPPER GROUPS T4C 1350 RRD BASEMENT * Insertion of ribbons from the left side of the machine * Main engines inside the base ADVANCEMENT BENCH * Motorized adjustment of the work surface with two-speed gear motor * Rear rubber-coated carpet drive roller * Automatic device for centering the conveyor belt * Input safety microswitch for excess thickness * Useful working width 1350 mm * Min. thickness and max. workable 3 ÷ 170 mm * Feed speed from 3.5 to 18 m/min OPERATING GROUPS * Belt oscillation with electronic control * Automatic disc brakes for quick stopping of groupsets PRESSURE SETS * Inlet grooved rubber roller equipped with safety device to prevent pieces from returning ELECTRICAL EQUIPMENT * Automatic star/delta starting on main engines * Magnetothermic protections on motors * Stabilized current power supply for electronic equipment EMERGENCIES / SAFETY * Hand protection strap at entry of pieces * Front and rear emergency mushroom switch * Lockable main switch * Automatic emergency stop of the machine in case of: - breakage of the abrasive belt - non-tensioned abrasive belt - lateral exit of the abrasive belt - opening of the access doors to the operating groups - lack of compressed air - motor overload BASIC MACHINE SY T5C 1350 * CARRYING BASE * * Control panel on the machine 1st OPERATING GROUP “R” R-CL 1350 * Calibrator/sanding roller assembly The group is equipped with: * Adjustment of the working position of the roller with indicator and pre-selection memory of the abrasive belt grain * Automatic brake for stopping the sanding belt in case of emergency * Automatic oscillation of the abrasive belt via electronic system * Abrasive belt rotating in the opposite direction to the advancement - Development of abrasive belt 1900 mm R250 Roller diameter 250 mm R85 85 sh rubber coated calibrator roller with abrasive belt speed of 24 m/sec Pneumatic ON/OFF of the roller made with a pneumatic activation cylinder complete with adjustment micrometric of the position of the roller as a function of the thickness of the abrasive belt Oscillating blower for cleaning the longitudinal abrasive belt The device is equipped with: - Operation of the swing with electronic system - Timed intervention activated directly by the piece being processed - Filter and pressure regulator 11 kW (20 HP) motor 2nd OPERATING GROUP “R” R-CL 1350 * Calibrator/sanding roller assembly The group is equipped with: * Adjustment of the working position of the roller with indicator and pre-selection memory of the abrasive belt grain * Automatic brake for stopping the sanding belt in case of emergency * Automatic oscillation of the abrasive belt via electronic system * Abrasive belt rotating in the opposite direction to the advancement - Development of abrasive belt 1900 mm R250 Roller diameter 250 mm R65 65 sh rubber coated calibrator/sander roller with abrasive belt speed of 18 m/sec Pneumatic ON/OFF of the roller made with a pneumatic activation cylinder complete with adjustment micrometric of the position of the roller as a function of the thickness of the abrasive belt Oscillating blower for cleaning the longitudinal abrasive belt The device is equipped with: - Operation of the swing with electronic system - Timed intervention activated directly by the piece being processed - Filter and pressure regulator 11 kW (15 HP) motor 3rd OPERATING GROUP “D” DP 4/16 1350* TRANSLATION GROUP WITH 4 ROTARY HEADS HOLDERING ABRASIVE BRUSHES Prepared for housing 16 brush discs with a diameter of 125 mm. SI/8/125 * Set of 16 rotary discs with a diameter of 125 mm SI/8/125 * Complementary set of 16 discs diameter 125 mm Electronic auto-set of the "DP 4/16" group for work positioning managed by the Hydra V-Pad electronic control 4th OPERATING GROUP “b” GS/200 1350 * OUTPUT BRUSH UNIT The device is equipped with: - Dust extraction hood - Adjustment of the working position of the roller - Rubberized pressure roller at entry and exit Cleaning roller with a diameter of 200 mm in Tampico 1.1 kW (1.5 HP) main motor · PRESSERS GP/M-E Pressure group with rubberized rollers and tip at entry to the 1st roller group GP/M-I Pressure group with rubberized rollers and intermediate tip between the 1st and 2nd roller group GP/M-U Pressure group with rubberized rollers exiting the 3rd roller group · WORK PLAN Carpet advancement with 3 kW inverter 60 sh rubber conveyor belt · COMPACT IN-LINE MACHINE DEVICES Machine in compact end-of-line version (lower/upper) with previous System B5C 1350. The entire compact line is managed by a single "Hydra V-Pad" control panel and a single "PLC" T4M base with worktop at a fixed height of 900 mm from the ground Predisposition for vacuum top (perforated top and carpet) for 2 modules Internal electric fan with 7.5 kW (10 HP) motor for 2 modules N° 4 independent floating shelves to compensate for differences in material thickness E) Connection transfer Transfer for the transit of the pieces towards the automatic loader of the INTEGRA cell composed of: - Motorized roller conveyor dim. 3800 x 1500 mm equipped with transverse belt frame for transferring pieces rollers-belts - Motorized roller conveyor dim. 4000 x 250 mm for sending solid pieces to Integra - Motorized belt frame dim. 2400 x 1500 mm for sending panels to Integra Predisposition for manual loading and unloading of solid wood pieces with lengths from 3200 to 6000 mm F) Loading/unloading bridge Loading and unloading bridge for work/processed pieces Composed of : - Pieces locking pliers - electronic vertical positioning - electronic longitudinal movement (loading/unloading benches and work surfaces) G) Tenoning, profiling and drilling/milling center mod. Integrate MACHINE COMPOSITION: WORK PLAN Each work surface is made up of clamps that allow the piece to be clamped according to its dimensions itself and to be able to carry out tenoning, drilling/milling and profiling on five sides. At the end of cycle an opposite gripper allows the exchange and processing of the sixth side. The system is double in order to be able to accommodate two rows of pieces and, depending on the length (max 1450 mm), up to four pieces. Easyset worktop (placed on one of the worktops) Motorized table automatically managed by CNC. Allows automatic positioning of bars and clamps (or suction cups) significantly reducing setup time. Ideal for processing pre-finished elements. Scrolling of the motorized bars and suction cup holder plates takes place entirely on prismatic guides to guarantee a high rigidity and obtain maximum finish. AXIS MOVEMENT brushless motors with digital drives prismatic sliding guides with pre-loaded ball bearing slides on all axes (X - Y - Z). X axis transmission with precision rack and pinion V max from 70 to 105 m/min Y axis transmission with precision rack and pinion V max 130 m/min Z axis transmission with ball screw-nut system V max 30 m/min automatic centralized lubrication system managed by numerical control VACUUM SYSTEM vacuum pump flow rate 90 m3/h UNITY OF GOVERNMENT numerical control NUM program memory 800 Kb maintenance of the thermal balance of the electrical components of the control unit via air conditioner PC OFFICE Microsoft Windows XP operating system 17'' LCD monitor Qwerty keyboard CELERON 2.8 GHz microprocessor 80 GB hard disk 512 MB RAM memory DVD-Rom player network card OPERATOR INTERFACE Xilog Plus - piece programming via graphic editor or free editor - automatic execution of the program - execution of multiple concatenated programs (MIX) - execution of machine commands in manual mode (MDI) - machine parameter configuration with password protection - management of subroutines and user macros - management of operator, diagnostic, run time and interactive messages - file report (production, diagnostic) - barcode management - import of DXF files - machining optimizer - tool tooling management - dynamic control of accelerations/decelerations Workpiece dimensions Max workable length. 3200 mm * on the same plane up to 2x1450 mm * using the two floors simultaneously (manual loading/unloading) 6,000 mm Minimum length (internal tenon) 206 mm Max piece height using Combiflex table 160 mm Using Easyset 100 mm plane Minimum piece height 30 mm Max working width 220 mm Minimum width 30 mm MACHINE COMPOSITION: Electrospindle HP 13 kW 7,000 rpm N. 2 ● HSK F63E tool holder ● rotation speed 100-12000 rpm ● left and right rotation ● max. power 13 kW (16 Hp) at 7000 rpm (in continuous service S1) ● grease lubrication ● forced circulation liquid cooling with heat exchanger N. 2 vector rotary axis - interpolating - with pneumatic users Rotating axis managed by CNC with continuous 360° rotation for optimal execution of all those processes such as drilling, blade cutting, horizontal milling and mortising which require the use of return heads angular - also special three-reference models with pneumatic users - oriented in different directions within the same piece. Adjustable chip conveyor for electrospindle and Prisma head It allows optimal cleaning of the work area by directing the jet of chips towards the suction mouth generated by the tool during milling. N. 2 Prisma HP: 5-axis electrospindle HP 13 kW7,000 rpm electrospindle with HSK 63 E connection - rotation speed 1000-18000 rpm - left and right rotation - max. power 13 kW at 7,000 rpm constant up to 18,000 rpm (in S1 service) - grease lubrication - forced circulation liquid cooling, with static inverter heat exchanger No. 4 Rapid 48 Technical data: ● 48 stations (tool holders not included) ● distance between stations 104 mm ● maximum weight per tool 15 kg (with (centre of gravity up to 110 mm from the tool shaft stop) ● maximum weight on the warehouse 300 kg - possibility of warehouse equipment: - Variable depending on the tool diameter - possibility of housing 2 tools on the same cone BRC: drilling, milling and cutting unit No. 1 Features: - Vector 360° rotary axis - blade diameter 300 mm for max 100 mm cut - N° 2 horizontal outlets for drilling - N° 2 horizontal outlets for ER25 milling -N° 1 vertical outlet for ER25 milling - handle hole: 3 vertical outlets 21.5 mm center distance - N° 2 vertical outlets 22 mm apart FX worktop - MATIC - H=110 Motorized table automatically managed by CNC. Allows automatic positioning of bars and clamps (or suction cups) significantly reducing setup time. Ideal for processing pre-finished elements. Scrolling of the motorized bars and suction cup holder plates takes place entirely on prismatic guides to guarantee high stiffness and obtain maximum finish. Plan composition: no. 2 fixed reference bars with 1 stop each. no. 5 mobile bars complete with nr. 2 suction cup holder plates and nr. 1 bar by reference each nr.10 covers for suction cup holder plates nr.10 suction cups Laser and reference stop for SX bows Reference stops H 110 N. 7 Nr. 1 additional lift H=110 N. 3 Additional Easyset clamp No. 10 Easyset additional clamp for short pieces No. 2 250 m3/h (5.5 kW) vacuum pump Laser piece marking device - vertical positioning of A.C. - horizontal positioning A.C. - rotation 0-180° H) Connection transfer Transfer for receiving the pieces from the Integra and unloading on the accumulation bench Composed of : N° 1 bench for parking machined pieces measuring 2500x 2000 mm N° 1 a 300 x 3500 mm motorized roller section I) Accumulation bench Piece accumulation bench N° 1 bench with motorized belts for parking machined pieces measuring 2500x 4500 mm